How to improve the thermal shock resistance of high alumina bricks?
High-alumina brick high-temperature furnace and thermal equipment commonly used one of the high-alumina refractory bricks, some parts of the rapid temperature or rapid changes in the temperature range of the region, which requires high alumina brick to have excellent thermal shock resistance.
First of all to understand what is thermal shock resistance?
Thermal shock resistance refers to the refractory resistance to sudden changes in temperature caused by the ability to damage, thermal shock resistance can also be called thermal shock stability, thermal shock resistance, resistance to temperature abruptness and resistance to rapid cooling.
For example: ladle in Sheng steel, pouring or pouring process, converter, electric furnace and other steel in the feeding, smelting, tapping or shutdown furnace temperature changes, other intermittent high temperature furnace or container in the intermittent process, due to The rapid changes in temperature, resulting in lining refractory material cracks, peeling or even damage, this damage is the kiln lining damage and one of the main reasons.
What are the technical measures to improve the thermal shock resistance of refractory materials?
(1) the choice of raw materials and admixtures: select the linear expansion coefficient of small, high thermal conductivity of raw materials, without affecting the performance of other refractory materials under the premise of the use of small linear expansion coefficient, high thermal conductivity of admixtures.
(2) Optimization of microstructure of materials: adding the second phase to the refractory material, using its phase change to produce microcracks to enhance the toughness and improve the thermal shock resistance.
(3) to meet the conditions of use under the premise of the size of the requirements of refractory bricks accurate.
How to improve the thermal shock resistance of high alumina bricks?
A high-alumina brick with a high bauxite clinker and fused white corundum powder as raw material, adding appropriate expansion agent, formed by the heat treatment and 800 degrees, can be made of high thermal shock resistance of high alumina brick. Its requirements are as follows:
(1) The chemical composition of the first grade bauxite clinker is: the content of AL2O3 is 83.5%, the content of sio2 is 9.39%, the content of fe2o3 is 1.29%, the content of K2O + Na2O is 0.86%
(2) fused white corundum powder 5% -10%
(3) andalusite and sillimanite composite expansion agent 6% -15%, chemical binder 6% -10%.
The kneading was carried out in a kneader, and 50% of the chemical binder was added to the coarse particles. The composition of the clay was as follows: 5-3mm18.4%, 3-1mm26.7%, 1-0.5mm3.5% , 0.5-0.1mm8.2%, less than 0.1mm43.2%, moisture 3%, sleeps 2H above.
Brick in the 300T friction Sassafras press molding, increase the number of pressure and the maximum impact to ensure the quality of brick, bulk density greater than 2.85g / cm3. Brick after 160 degrees drying, in the torch furnace firing temperature of 1430-1450 degrees, holding time 40H.
The physical and chemical indexes of this kind of high alumina brick are as follows: al2o3 content 78%, sio2 content 12%, fe2o3 content less than 2.2%, apparent porosity less than 21%, room temperature compressive strength 70MPA, load softening temperature 1550 Degree, heat shock type (1100 degrees, water cooling) more than 10 times, can be used for 5T electric furnace top, no peeling, out of the phenomenon.
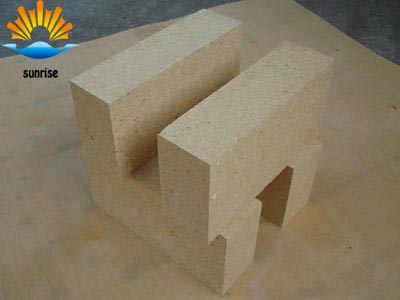